Resistance brazing and soldering
Resistance brazing – material-to-material connections for large cross-sections
Resistance welding under braze can be used to reliably join divergent joining partners (in terms of geometry and material properties). It is also suitable for the connection of large cross-sections. In general, welding under braze can be carried out either in an overlapping or butt welding process.
Butt welded connections have the following advantages:
- reduction of the connection height to the thickness of the terminal, while the construction height for overlap welding corresponds to the height of both welding partners,
- a significant reduction in compacting length (material savings),
- a considerable reduction in contact part length (material savings and advantages during punching),
- almost no heat input,
- hardly any wear on the electrodes,
- tensile forces at least at the same level as for overlap welding,
- excellent monitoring capability (equal to overlap welding),
- no formation of bulges at the joint in the STRUNK process (no post-processing required),
- almost no contact resistance and
- preservation of all features of resistance welding.
20 years of experience in resistance brazing
Process development with joints welded under braze has been part of our portfolio for two decades. It started with an order from an OEM to develop an application with which oily punched brass parts could be welded with a braid. The previously used joining processes led to field failure and were therefore unusable.
We suggested adding a braze plate between the joining partners to create a resistance connection in a reliable process. In order to industrialize the braze supply, we developed our first automated braze feeders for welding processes. We have been continuously optimizing these systems ever since.
When the first intelligent battery sensors (IBS) were installed in the 12 V electrical system of vehicles, this process was already in use. It was being applied to weld the measuring shunt to the battery terminal, to terminals or cables, in manual to fully automated production. Today, almost all connections in the HV sector (cabling and connectors), power train and power distribution (busbars and EV wiring systems) are also industrialized using this technology.
Resistance welding under braze is also suitable for the following cases:
- The difference in material thickness between the joining partners is so great that regular resistance welding cannot be applied.
- In terms of melting temperatures, the joining partners differ significantly (e. g. copper and brass alloys).
- The application requires large-area connections (busbars) for which projection welding does not offer sufficient current carrying capacity. With resistance welding under braze, the joining partners can be connected over a largely homogeneous surface. This has a positive effect on the current conductivity.
- Cables with large cross-sections need to be connected to terminals (e. g. CuFe) in an extremely conductive manner.
- The welding process must be carried out with lower machine power. This means that a concentration of energy is required from the added braze, which increases the contact resistance before welding and then alloys with both joining partners by melting.
In all cases mentioned, resistance brazing results in an indestructible connection with a contact resistance of almost zero.
We are your reliable partner for resistance welding under braze
Our current integrated servo braze feeders deliver a precise and reproducible amount of braze using servo technology and a multi-roller principle. This ensures:
- precise and reproducible positioning of the braze between the joining partners,
- straight-line feeding even over long distances through shaping measures,
- integrated monitoring of the amount of braze applied between the joining partners as a counter-check to the amount fed and
-
a punch cut to align the parameterization of the welding equipment to the joint and not to the burning off of the braze.
Our control systems are fully integrated via independent software function modules, both in the welding current control and in the machine control. The feeders with gripper system are suitable for right-hand and left-hand installation. Furthermore, they are mounted on quick-change couplings with Harting plug connection, which enable a quick changeover to a different width. Flat materials with a cross-section of more than 0.05 mm² can be fed in.
By feeding in the braze, we achieve a current concentration at the desired location. Under the application of a short and strong welding current, the materials fuse together to form a material bond that can only be separated by destructive means. This process can be used to weld materials with differing cross-sections as well as busbars together. Connectors or busbars used may also be coated.
Our systems are not designed for mere brazing (i. e. melting of the brazing alloy). Instead, as with projection welding, they are designed with high power and high rigidity to achieve the shortest possible welding time under very high welding currents. In this way, we generate high holding forces of the joint. The contact resistance can be lower than the bulk resistance of the material (depending on the material). For example, pull-off forces of more than 10,000 newtons can be achieved with larger cross-section cables.
Our offers for resistance welding under braze
We are able to industrialize and automate a very high proportion of applications because we can use the process in the following ways:
- Direct application of braze between the joining partners using the automatic STRUNK servo braze feeder:
-
- between two busbars/components,
- between a compacted strand and a terminal or a busbar as well as
- between a non-compacted strand and a terminal or a busbar (ALL IN ONE SHOT solution).
-
- Pre-soldering of joining partners using automatic STRUNK feeding technology or manual feeds for manual workstations:
-
- pre-soldering of busbars and
- pre-soldering during a compacting process (only in case of partial or full automation[Referenz] due to the orientation; if the reference is lost, the orientation needed can be achieved manually in a second step using a marker).
-
With our practical solutions for resistance brazing, you can meet the high technical requirements when joining workpieces and materials that are difficult to connect. Use our experience from more than 50 years of process technology to master your challenges in the area of resistance soldering and gain an edge over your competitors.
Overlap welding
(customer-specific solutions as an example)
Cable-to-terminal connections
Welding of busbars
Semi-automatic systems
Automatic systems
Butt welding
(customer-specific solutions as an example)
Concepts for manual production
Pre-soldering
(customer-specific solutions as an example)
Compacting under braze and welding to terminals
Pre-soldering of busbars/terminals/connectors
This automatic system with four servo-controlled axes and a tool changing system is suitable for different products. It contains STRUNK medium-frequency welding tongs (1000 Hz) and a STRUNK servo braze feeder for precise positioning of the braze pad on the busbar.
Automatic machines for module connectors
Linear transfer (customer-specific solutions)
Transfer lines for compacting and punching as well as for overlapping or butt welding of braid strands and HV wire sets
Here you can see a fully automatic transfer line for compacting, punching, and overlap welding or butt welding of braids and HV wiring sets. This automatic lateral transfer machine for module connectors can be adjusted to cable lengths of 150 mm to 2000 mm. Single and double-stranded cables may be used. With our intelligent STRUNK CLAMPING system, even cables of different lengths can be joined in the connector. The cable ends are processed simultaneously on both sides. Finished products are output to a conveyor belt, sorted or unsorted, depending on further processing and automation strategy. These systems are reinforced for large-area compaction and connection surfaces.
Turntable systems (customer-specific solutions)
Turntable systems for butt welding module connectors
We offer automatic turntable systems for butt welding for module connectors made of braids and HV cables. Its 18 available types are set up for Poka Yoke and monitored. This machine is adjustable to cable lengths from 150 mm to 2000 mm to process single cables and double-stranded cables. With our intelligent STRUNK CLAMPING system, even cables of different lengths can be joined in the connector. The cable ends are processed simultaneously on both sides. Finished products are output to a conveyor belt, sorted or unsorted, depending on further processing and automation strategy.
Samples
Busbar application for power distribution in HV busbar wiring systems
Connections from busbars to contact elements (HV connectors), HV cables and braids can be welded.
Busbar application for power distribution in HV busbar wiring systems
Connections from busbars to contact elements (HV connectors), HV cables and braids can be welded.
Busbars in injection molding – application in the area of power distribution, large-area connections between connector part and busbar
Connections from busbars to contact elements (HV connectors), HV cables and braids can be welded.
STRUNK semi-automatic double head transfer for HV connectors
Connections from busbars to contact elements (HV connectors), HV cables and braids can be welded.
Welding of battery terminals on copper busbars, application in fuse box
Connections from busbars to contact elements (HV connectors), HV cables and braids can be welded.
Welding of battery terminals on copper busbars, application in fuse box
Connections from busbars to contact elements (HV connectors), HV cables and braids can be welded.
STRUNK semi-automatic double-head transfer for compacting under braze and welding onto pipes
Compacting under braze and automatic transfer of the compacted cable enables welding onto the pipe without deforming it.
Copper cable to busbar, welded under braze as an ALL IN ONE SHOT solution
The cable is compacted and welded onto the contact using our automatic braze feed.
Welding under braze of cables or busbars to intelligent battery sensors (IBS)
The cable is compacted and welded onto the contact using our automatic braze feed.
Welding under braze of cables or busbars to intelligent battery sensors (IBS)
The cable is compacted and welded onto the contact using our automatic braze feed.
Busbars in injection molding – application in the area of power distribution, large-area connections between contact part and busbar
We are looking forward to seeing you!
STRUNK Connect automated solutions GmbH & Co. KG
Siegtalstrasse 20
D-57548 Kirchen-Freusburg, Germany
Phone: +49 (2741) 93 87 10 – 100
Fax: +49 (2741) 93 87 10 – 199
Email: info@strunk.de
next upcoming trade fair
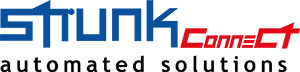